Kompetenzen
Sie benötigen eine Lösung? Wir hätten da jahrelange Erfahrung für Sie.
Wir begleiten unsere Kunden bei den täglichen, aber auch bei den besonderen Herausforderungen der Medizintechnik. Wir begeistern unsere Kunden durch Verbindlichkeit, Zielstrebigkeit, Authentizität, Kreativität, Ideenreichtum, Leidenschaft für Kunststoff und eine optimale Umsetzung.
Maßgeschneiderter Service
Unser Standard: individuelle Betreuung
Als Experte und Systemlieferant medizinischer Kunststoffprodukte legen wir höchsten Wert auf Präzision, Reproduzierbarkeit und Hygiene.
Wir möchten für jeden Kunden und seine Bedürfnisse eine maßgeschneiderte Lösung erarbeiten. Dabei legen wir höchsten Wert auf Transparenz und die Einhaltung gemeinsam gesteckter Ziele sowie Termintreue. Bei all unserem Tun verlieren wir allerdings nie den wesentlichen Kern unserer Arbeit aus den Augen: die Verbesserung der Gesundheit und Lebensqualität von Patienten. Mit unseren überdurchschnittlichen Serviceleistungen helfen wir unseren Kunden und Anwendern, anderen zu helfen.

Projektmanagement
Wir sind für unsere Kunden ein Partner auf Augenhöhe und setzen Wünsche und Ideen leidenschaftlich um. Wissenstransfer, Transparenz und Kommunikation sind uns besonders wichtig, um für jeden Kunden das beste Ergebnis zu erzielen. Um in kurzer Zeit das Optimum für unsere Kunden zu erreichen, lokalisieren wir zu Beginn sämtliche Problemstellungen und definieren bereits im Vorfeld spezifische Aufgabenstellungen. Für höchste Transparenz binden wir unser digitales Dokumentenmanagement in die komplette Prozesskette ein. Dadurch sind Ergebnisse und Fortschritte sofort und auch langfristig verfügbar.
Bei der Entwicklung neuer Produkte ist unser oberstes Ziel, die Anforderungen und den Verwendungszweck lückenlos zu verstehen. Nur so kann ein Ergebnis entstehen, das für Anwender und Patienten gleichermaßen faszinierend ist und bei dem potentielle Risiken minimiert oder gar eliminiert werden können. Im nächsten Schritt erfolgt eine FMEA-unterstützte Einzelbetrachtung von Funktionen und Schnittstellen. Diese hilft uns, mögliche Fehlerquellen frühzeitig zu erkennen und zu vermeiden.
Unser Entwicklungsprozess ist angelehnt an die VDI 2221 und wird unter anderem durch Methoden wie „Black-Box“ und „Ishikawa“ unterstützt. Entwicklung, Spritzgussformen-Management, Formenbau und Spritzguss-Know-how kommen bei wezi-med aus einer Hand. Patienten und Anwender stehen bei uns immer im Vordergrund.
Spritzgussformen
Am Anfang unserer Arbeit liegt unser Blick auf potentiellen Risiken für Patienten und Anwender, die durch die Form entstehen könnten.
Erst wenn alle Blickwinkel analysiert wurden, beginnen wir mit dem zweiten Schritt: der Entwicklung und Erstellung einer für die Spritzgießfertigung ausgelegten Spritzgussform. Entsprechend der Anwendung eines Bauteils und der daraus resultierenden Anforderung an Sauberkeit bieten wir eine schmiermittelarme und wahlweise auch komplett schmiermittelfreie Form-Auslegung an. Dabei kommt unseren Kunden das gesamte Weber Gruppen Kunststoff- und Spritzguss-Know-how aus vielen Jahrzehnten zu Gute. Wenn Schmierstoffe oder Beschichtungen zum Einsatz kommen, sind diese für die speziellen Anforderungen ausgelegt und selbstverständlich für den Einsatz in der Medizintechnik zugelassen.
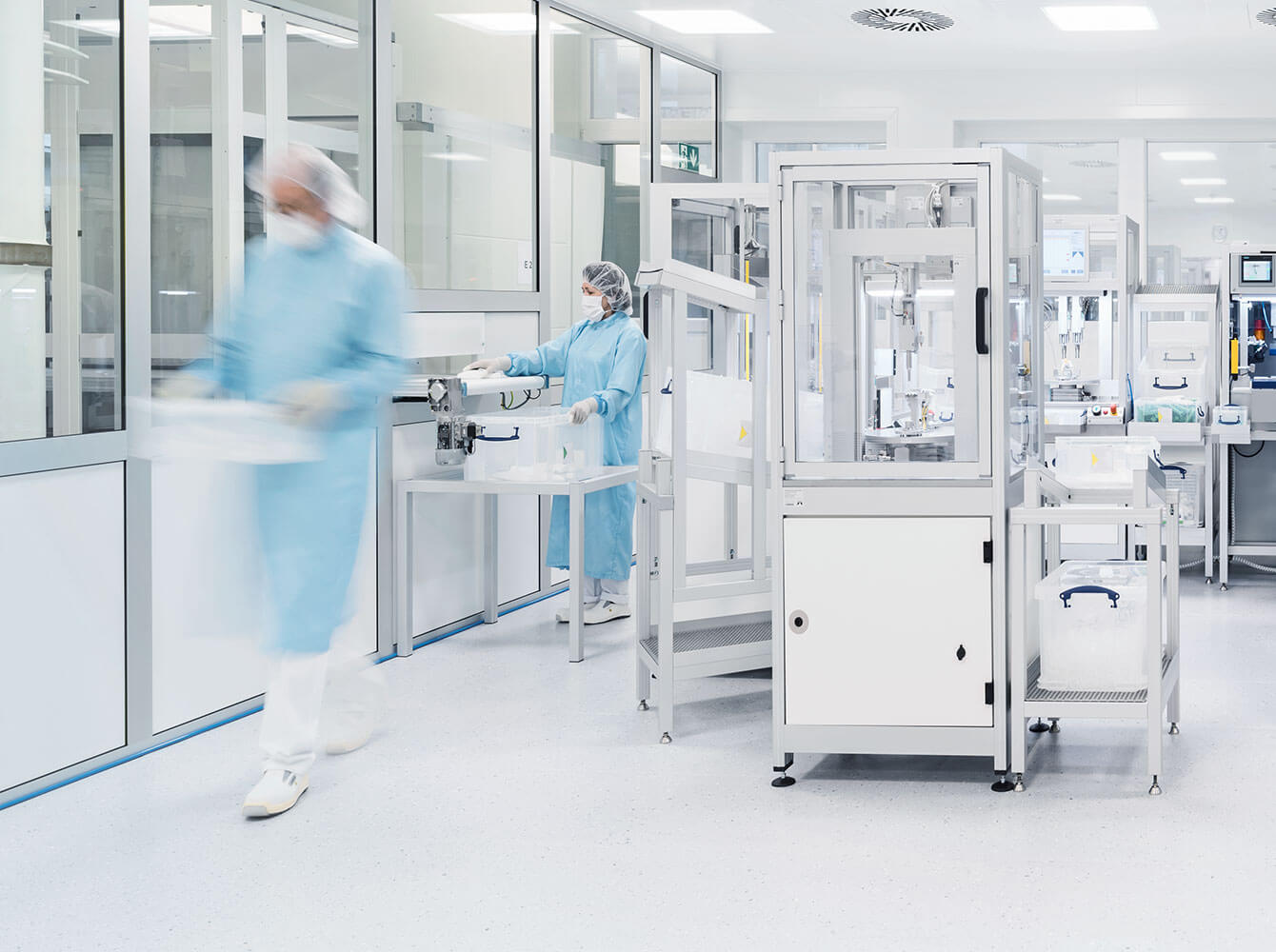
Reinraumfertigung
Reinraumfertigung State of the Art – dafür steht wezi-med. ISO Klasse 8, qualifiziertes Fachpersonal und effiziente Arbeitsprozesse garantieren durchgängig höchste Qualität. Um unseren Kunden zu jeder Zeit und bei jedem Projekt maximale Produkt- und Dienstleistungsqualität zusichern zu können, fertigen wir in Anlehnung an die GMP-Richtlinie. Auf diesem Weg gehen bei uns Vertrauen und Sicherheit immer Hand in Hand. Die Produktionsfläche des Geschäftsbereiches wezi-med verfügt aktuell über 400 m², davon beträgt die Reinraumfläche 125 m². In ihr werden Schweiß-, Montage- und Verpackungsprozesse durchgeführt. Die Kunststoff- Spritzgussmaschinen umfassen Kapazitäten von 280 bis 2.000 kN und sind im Satellitenprinzip direkt an den Reinraum angebunden. Das Handling der Spritzgussteile und die Zuführung in den Reinraum erfolgen vollautomatisch.
Die Fakten unserer Reinraumfertigung für Sie auf einen Blick:
- 125m² Reinraumfläche
- ISO Klasse 8
- Spritzgießmaschinen von 280 bis 2.000 kN, davon 1100 kN 2K
- Vollautomatische Entnahme und Zuführung der Spritzgussteile in den Reinraum
- Schweißen, Montieren und Verpacken komplexer Bauteile
- Validierte Prozesse

Analyse
Bei einer Kundenanfrage werden bei wezi-med zunächst eine Reihe von Parametern überprüft. Im ersten Schritt gibt es die Machbarkeitsprüfung. Hier wird ermittelt, ob eine kunststoffgerechte Produktentwicklung überhaupt möglich ist. Darauf folgt die Prüfung, ob das Produkt mit einer Spritzgießmaschine herstellbar ist. Fallen diese Punkte positiv aus, erfolgt die Materialauswahl und die Ermittlung, ob der Folgeprozess im Reinraum umsetzbar ist.
Kunststoffspritzguss
Kunststoff-Know-how seit 1959 – das bedeutet die Kreation und Entwicklung immer besserer und innovativerer Produkte und Lösungen. Dabei geben wir uns nie mit dem Status quo zufrieden. Wir optimieren und verbessern unsere Prozesse kontinuierlich. Nur so ist es möglich, unseren Kunden nicht nur maßgeschneiderte Lösungen nach ihren Vorstellungen zu bieten, sondern immer auch einen zusätzlichen Mehrwert, den unsere Kunden so noch nicht kannten. Dies können wir sowohl in Ein- als auch in Zwei-Komponententechnik.
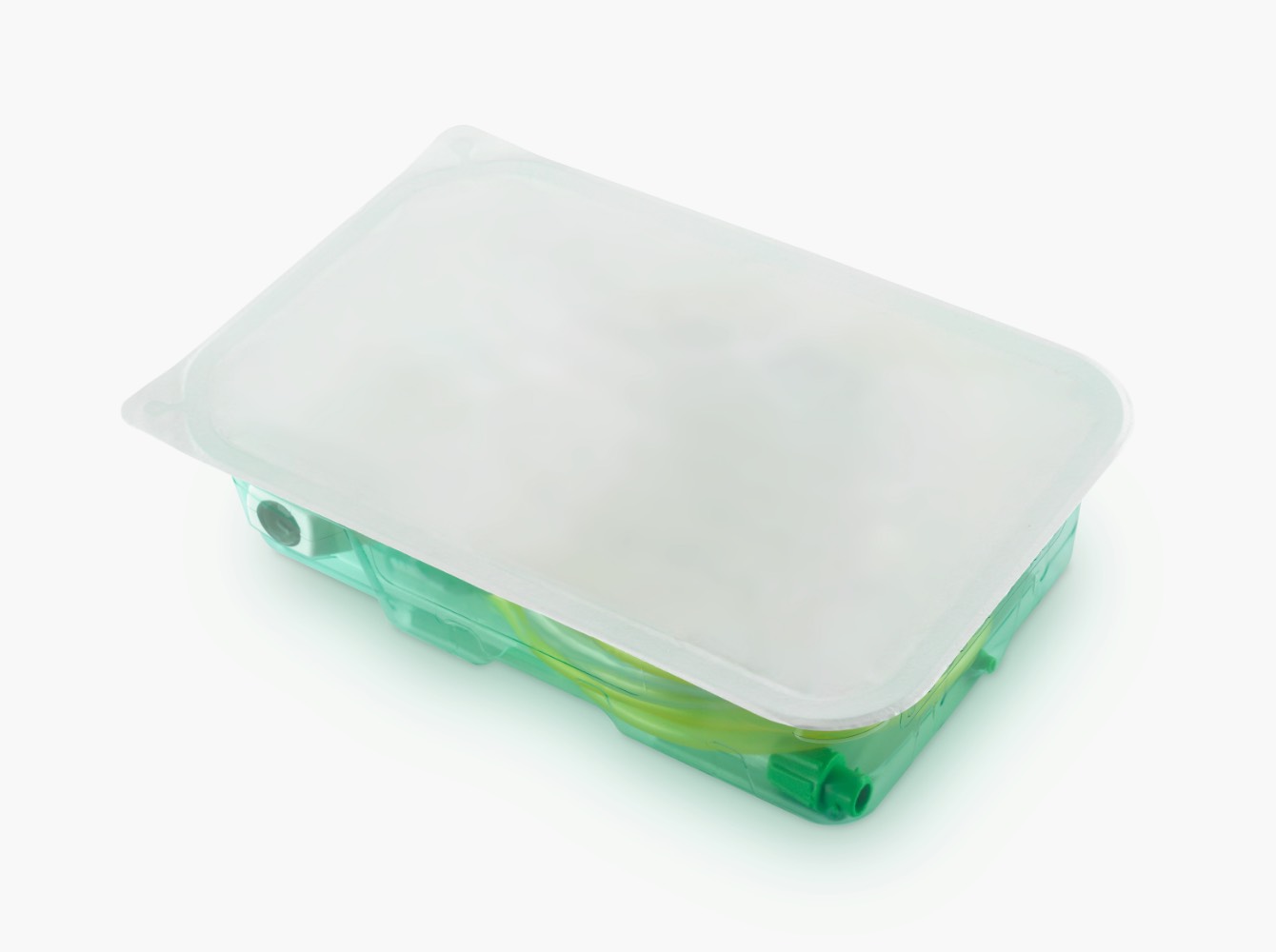
Verpackung
- Versiegelung von Blister und Tyvekfolie mit Siegelmaschine im Reinraum
- Labeling nach Kundenanforderungen mit CAB-Drucker und Easylabel-Software
- Rückverfolgung der Produkte über Barcode/QR-Code und UDI
- Blisterpack, Peel-off-Tyvekfolie und Labeling erfolgen nach Kundenvorgaben
- Validierung und Protokollierung der Prozesse über die Qualifizierungsphasen DQ, IQ, OQ und PQ
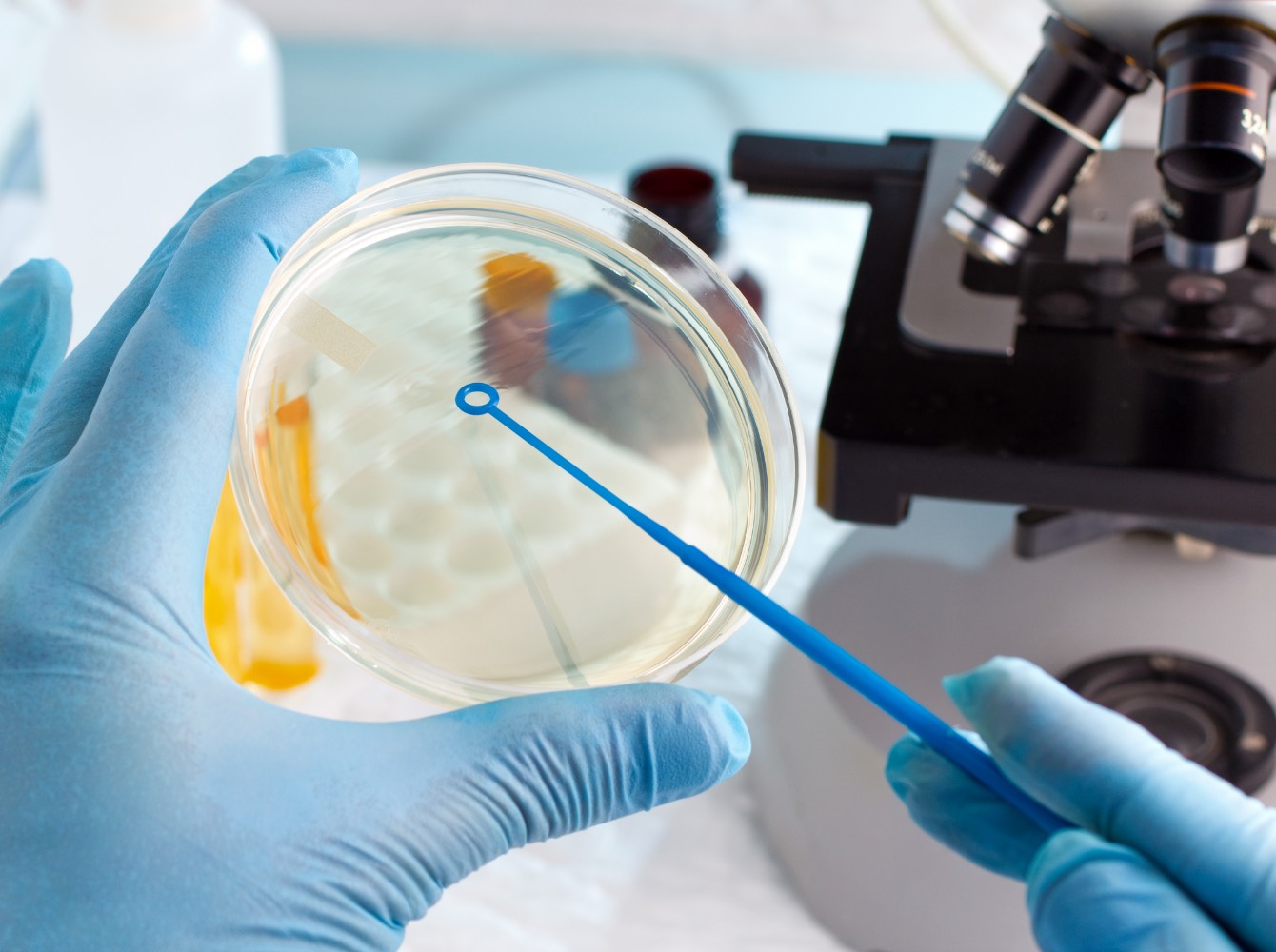
Sterilisation
In Zusammenarbeit mit renommierten nationalen Geschäftspartnern bieten wir verschiedene Sterilisationen für Medizinprodukte an.
Dabei wird für jeden Anwendungsfall das beste Sterilisationsverfahren ermittelt, um ein Höchstmaß an Sicherheit zu garantieren. Im Rahmen der Reinraumproduktion legen wir bereits frühzeitig - durch mikrobiologische Kontrollen und die Anwendung eines wirksamen Hygienekonzepts - die Basis für eine zuverlässige Sterilisation. Hier eine Übersicht der von uns angebotenen Sterilisationsverfahren:
- Sterilisation mit Ethylenoxid
- Elektronenstrahl-Sterilisation (E-Beam)
- Beta- und Gammastrahlen-Sterilisation
- Dampf-Sterilisation